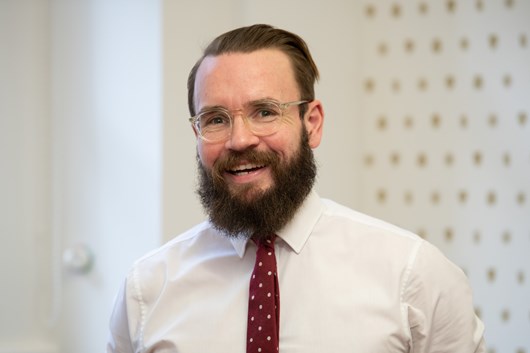
Management Team
Will Evans
Watch Will in our Security video below.
Director (Assay Master)
How did you begin your career at the Assay Office?
I started work in the laboratory as Lab Assistant in 2000, replacing an employee who had been lab assistant for over 40 years. It was then put to me that I could be lab assistant for 40 years too or I could do some further education. Due to the growth of non-destructive testing and the downturn in Hallmarking seen at that time, I decided to pursue a long held interest in computing, and studied for a degree in information systems and management, this lead to a move out of the laboratory and put me on the path to my current position. I was made Process Development Engineer in 2007, then Systems Development Manager in 2010, before being made Technical Manager in 2015, then Superintendent Assayer in 2017. I was made General Manager in summer 2021.
As long as we continue to find ways to marry the latest technological advances with our 700 year old traditions, I think the Assay Office will continue to remain relevant to its customers, and I hope to remain part of that.
What does your typical week involve?
First job on Monday is the weekly production report, which shows the Assay Office performance compared to the same period last year, in terms of articles Hallmarked and income generated across our five sites, this often sets the tone for the week, if the numbers are good then everyone’s happy.
Weekly Managers meetings ensure everyone is up to date with the various activities.
I will then check in with the teams I am responsible for to ensure the smooth running of the departments, although due to the high experience levels within them, this tends to happen without any involvement from me!
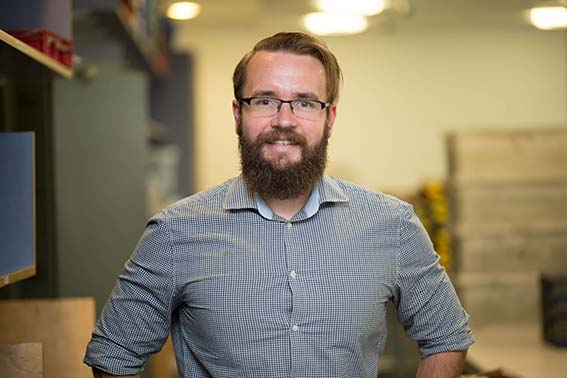
The rest of the week is then project dependent, discussions around the latest IT project, analysis for the board, maintaining our UKAS accreditation.
What has been your career highlight to date?
It has to be the project which lead to our engineering workshop bringing the production of every hallmark and sponsor’s punch used in the Assay Office back in house, which has led to us producing around 2000 punches per year in the basement of a listed building in the middle of the City of London.
Also, the first Hallmark punch produced on our laser was used to Hallmark the medals for the 2012 London Olympics.
For me this project sums up the Assay Office ethos of marrying cutting edge technology, in this case 3D laser engraving, with the traditions of the company and experience of the staff, all trained via the traditional apprenticeship method.
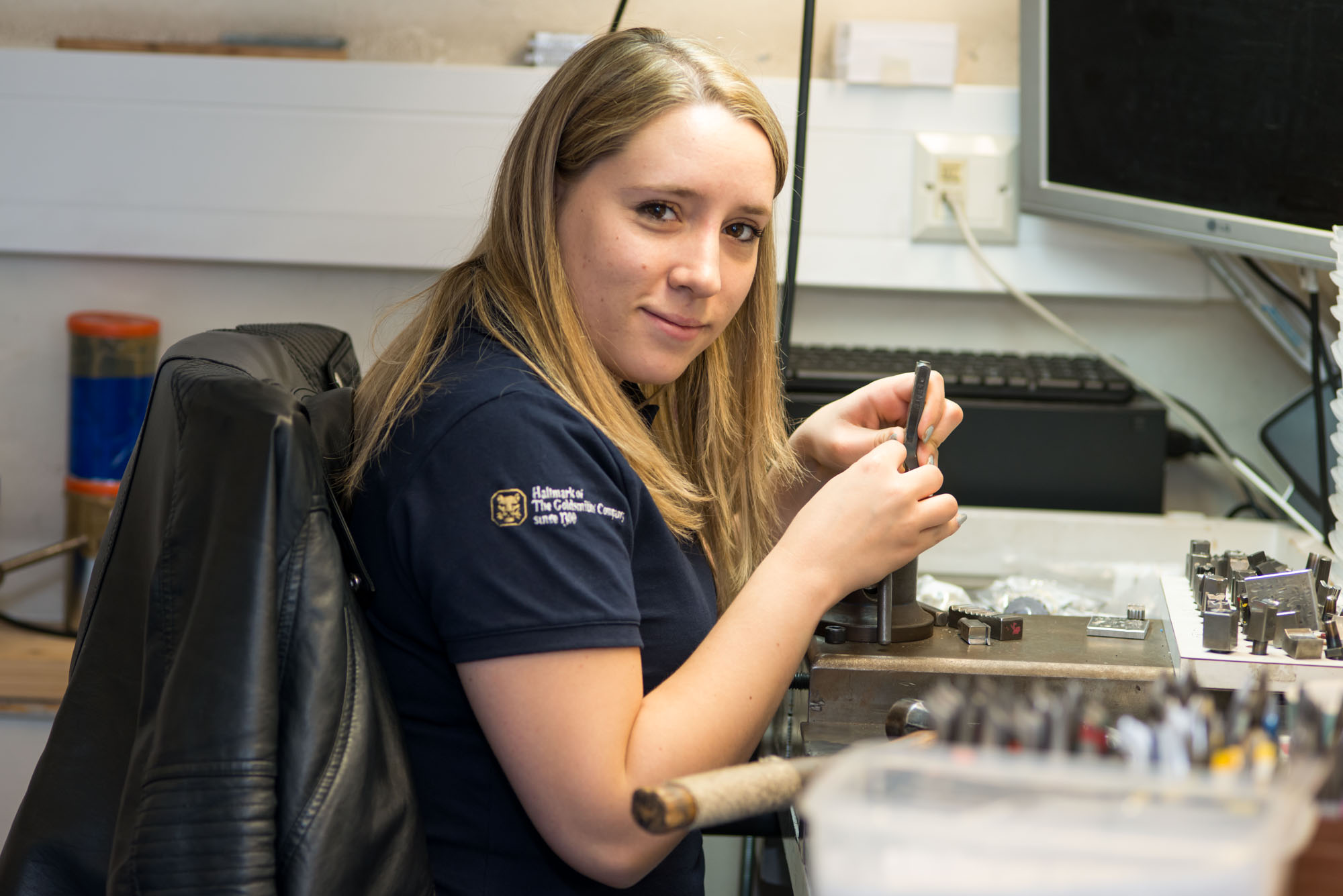
Kheni Priest
Production Control Manager
Kheni has worked for us since 2007. She began as a temporary staff member, moving on to a role as Hallmarking Technician, before being promoted to Supervisor at Greville Street in 2019 which she described as “a career highlight”.
She was promoted to Production Control Manager in 2022. General Manager Will Evans said “Kheni has a great connection to the trade in Hatton Garden, and a real energy and passion for it. This, along with her ambition and expertise is unmatched. Congratulations to her on this promotion.”
Adam Phillips
Deputy Director
Many of our customers will have spoken to our Account Manager, Adam Phillips. Adam has been working at the Assay Office for 21 years.
Describe a typical working day.
Busy, engaging and varied. Overseeing multiple departments and maintaining the turnaround times our customers desire, and which we want to give, is hard work but rewarding. I liaise with customers about the hallmarking process, often finding solutions to any problems they have and helping them to maintain their schedules. Occasionally I get time to go back to the work bench, where I do help out if we are busy. I especially enjoy going back to my favourite job on the bench, which is Handmarking.
What’s the best thing about working at the LAO?
The history and tradition that we are part of and the fact that we are doing something that will be looked at in hundreds of years’ time.
What is your top tip for customers who are sending in items for hallmarking?
Be precise about the mark you want. Understand what type of mark you are asking for and if it is indeed appropriate.
What’s your favourite fact about hallmarking?
Just having a 750 or a 925 stamped on an article is NOT a hallmark. I’ve lost count of how many times people find out my job and tell me that their piece of jewellery is hallmarked because it has those numbers on it!
What has been your most memorable moment here?
Becoming a Freemen of the Company and the City. To be part of this wonderful city’s tradition and expanding my horizons within the Livery movement has been most memorable.
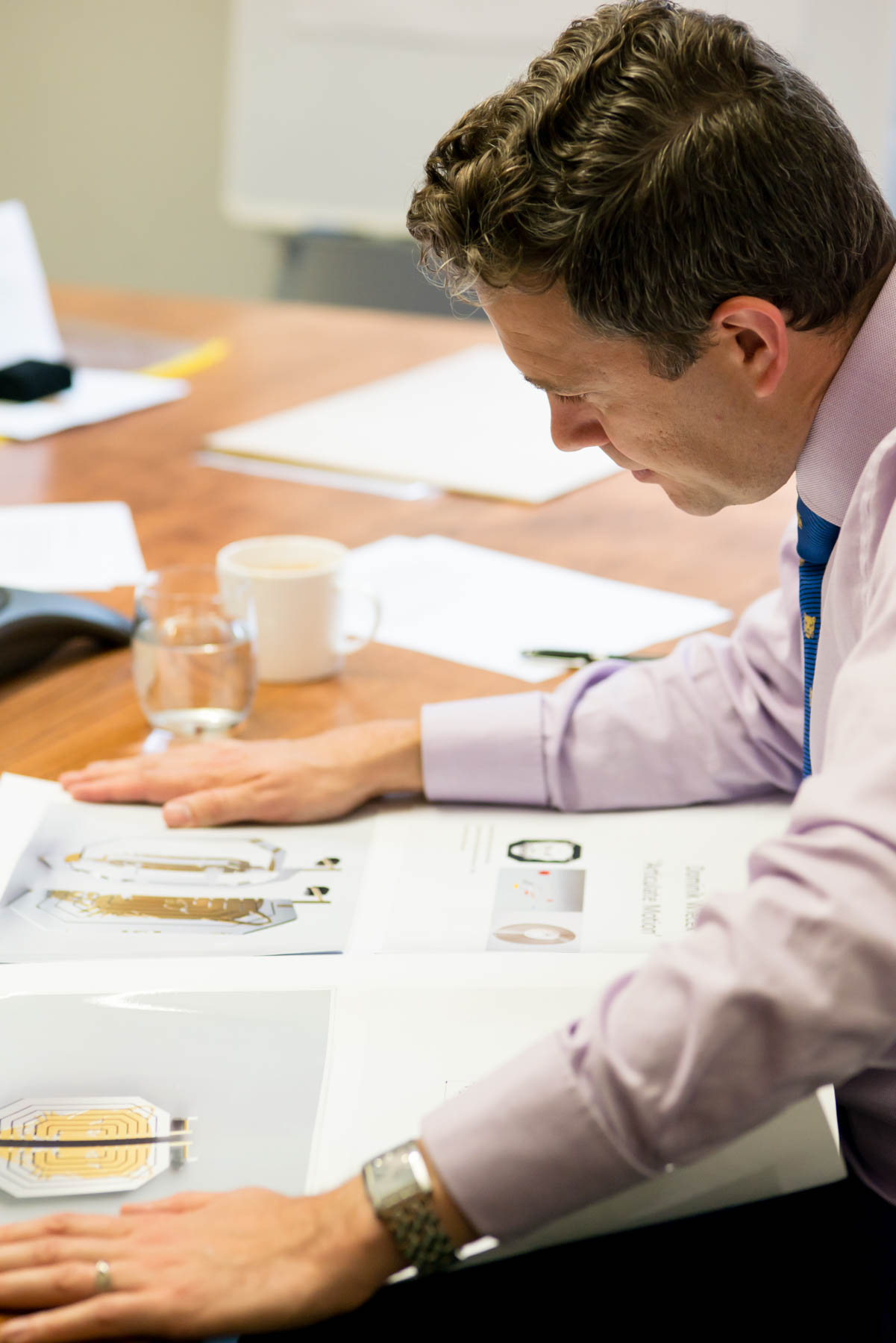
Read Adam's Q&A about Creative Hallmarking here.
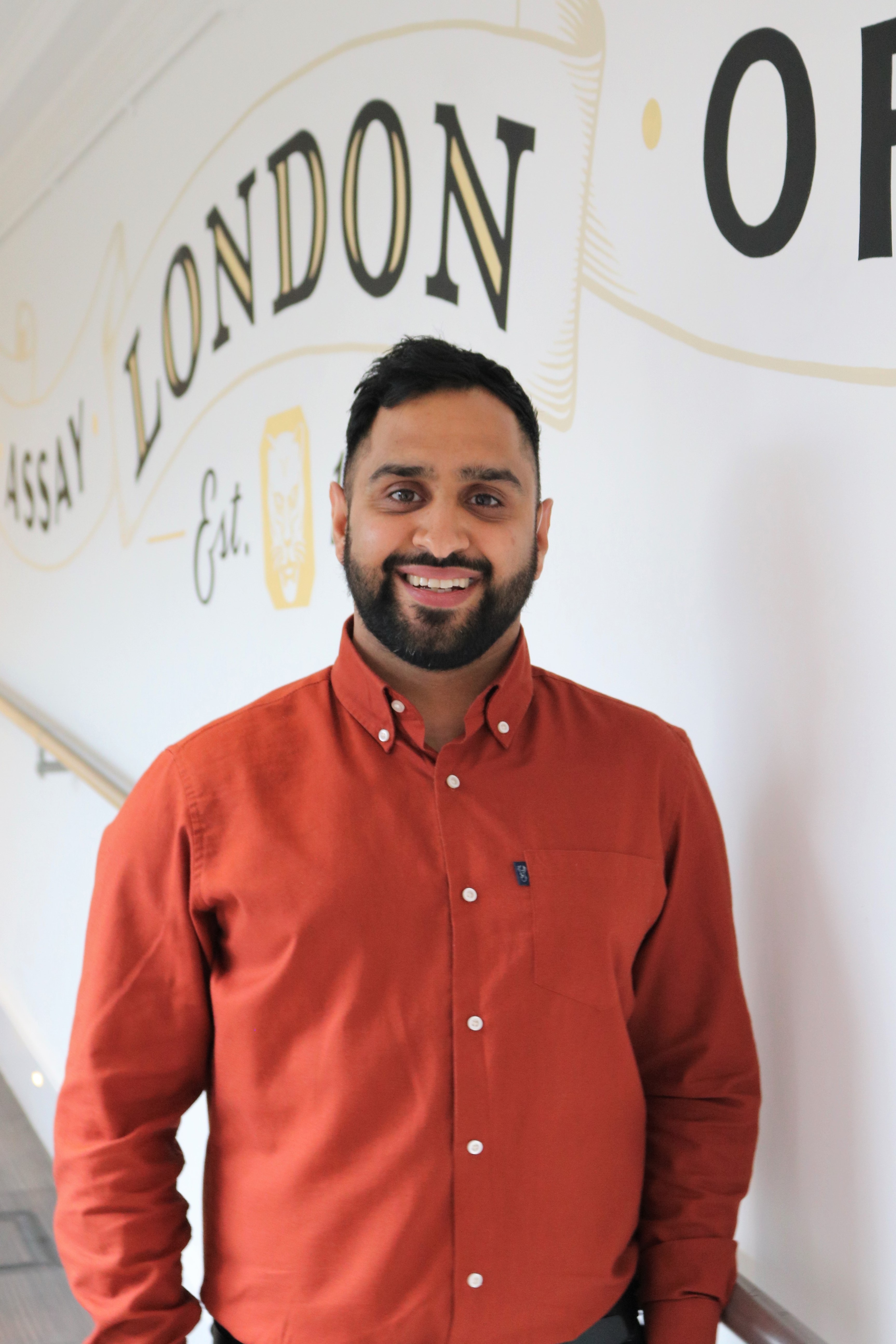
Raj Thaker
Technical Quality Manager
Raj started work at the Assay Office in January 2023. Below he answers some questions to introduce his role:
You have already been busy at the Assay Office, what has been your main focus so far?
I am ensuring that our services meet quality standards and customer requirements. My main focus is on maintaining and improving the quality of our technical processes used in our service delivery to ensure customer satisfaction and success. To achieve this I have been getting ready for our ISO 9001 audit and later, our ISO 17025 audit.
ISO stands for International Organisation for Standardization. ISO is an independent, non-governmental, international organization that develops and publishes international standards to ensure consistency, quality, safety and efficiency across products, services, processes and systems. Having ISO accreditations helps us to operate more efficiently and effectively and in turn increase customer satisfaction.
We have two ISO certifications which are:
- ISO 9001 – This outlines the requirements for a Quality Management System – this standard focuses on policies, procedures and processes for delivering services that meet customer requirements and comply with applicable regulations.
- ISO 17025 – This outlines the requirements for the competence of testing and calibration laboratories. We have to make sure that all activities such as sample preparation, testing, data analysis and reporting are performed in a reliable and consistent manner. This is for reassurance to our customers and stakeholders that we are competent and capable of providing accurate and reliable results.